Une meilleure communication, un planning collaboratif, une plus grande remise en cause et surtout, beaucoup de post-it. Voici quelques outils, peu habituels, du “lean”. Depuis quelques années, ce mode d’organisation dont la principale activité est la chasse au gaspillage séduit les entreprises et se répand bien au-delà de l’industrie, secteur où il est né. Focus sur le petit dernier : le lean construction.
Industrie, technologies de l’information, design, distribution… La méthode “lean management” semble si imparable qu’elle s’applique – à quelques exceptions près – à toutes les sauces. C’est donc sans grand étonnement que le secteur du bâtiment s’y est intéressé, il y a quelques années de cela – un peu moins de dix ans. Depuis, les initiatives mettant à profit ces principes au sein des entreprises et sur les chantiers, ne cessent d’abonder. Bien que ce concept soit encore mal connu et peu répandu, la demande en formation est, quant à elle, en perpétuelle augmentation.
Made in Japan
Mais avant de parler de “lean construction”, n’est-il pas nécessaire de revenir un court instant sur le terme “lean” ? Rétrospective : cette méthode trouve son origine au pays du soleil levant, dans les années 50, lorsque Taïchi Ohno met au point son système de production Toyota Production System (TPS). Alors inconscient de son avant-gardisme, le constructeur automobile japonais avait entièrement repensé son cycle de production, dans le but d’éliminer les pertes de temps et les activités considérées comme inutiles pour chaque étape de la chaîne, afin de pouvoir mieux se concentrer sur la satisfaction du client. De l’anglais lean qui signifie « maigre », « sans gras » ou encore « dégraissé », le terme naît de la bouche de chercheurs du MIT, James Womack et Daniel Jones qui, dans leur livre La machine qui a changé le monde (1990), souhaitait qualifier le système inspiré des méthodes de production de Toyota. Si l’expression “lean construction” est formulée pour la première fois en 1993, par l’International Group for Lean Construction, il faudra redoubler de patience – environ une vingtaine d’années – pour que le concept émerge en France, et s’y installe de façon pérenne. Aujourd’hui, l’école “lean” se voit encouragée par la constitution de réseaux comme l’Association Lean Construction (Aleco) ou encore l’Institut français de la Construction Lean.
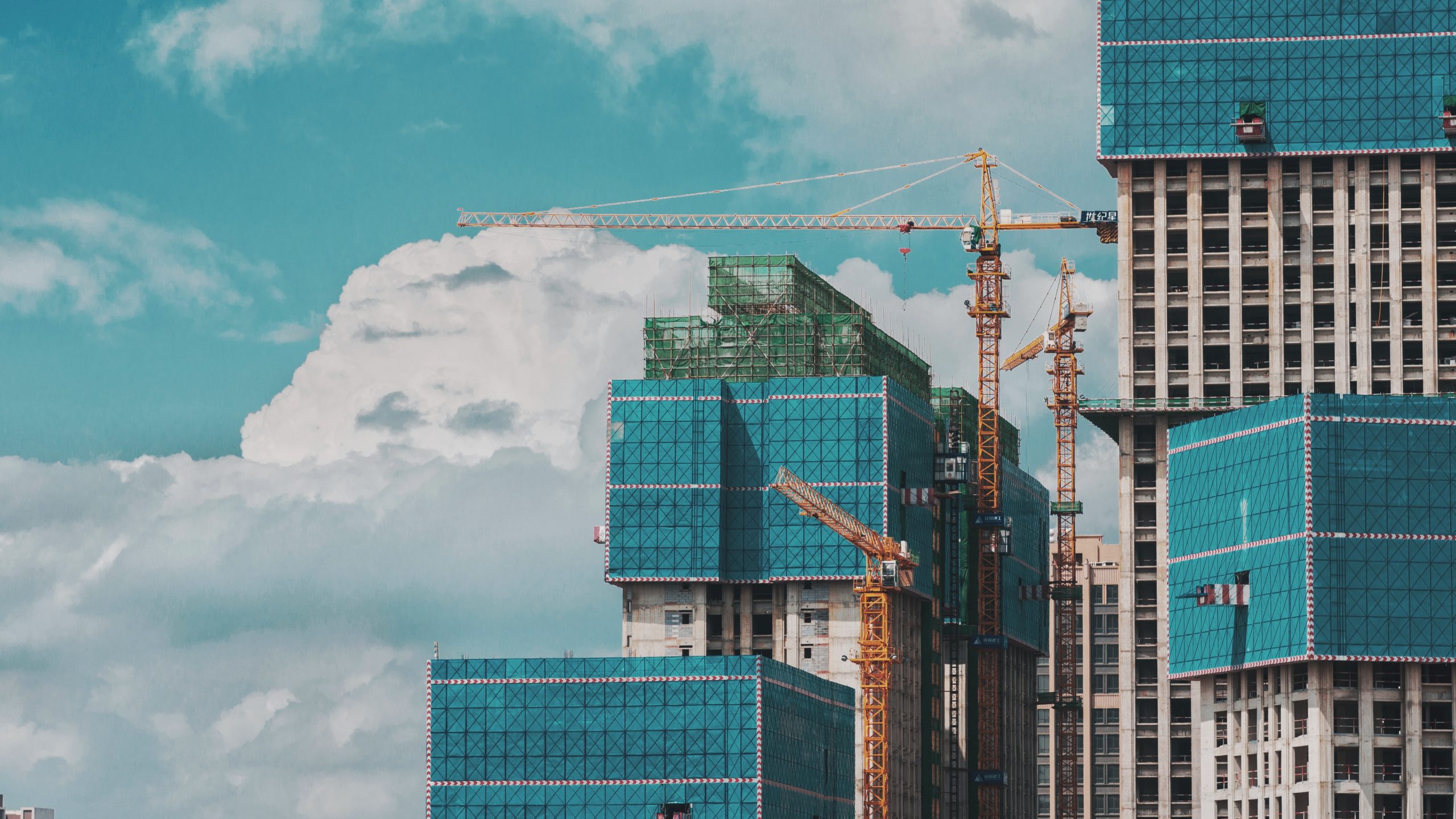
© C. Dustin
De cinq à sept
Comme à peu près tous les termes abstraits, le lean a pour fâcheuse manie d’inquiéter les entrepreneurs. Ce concept repose pourtant sur des principes tout à fait concrets. Ils sont au nombre de cinq : se mettre du côté du client, favoriser l’écoulement des flux, ne produire que si le client l’a explicitement demandé, viser la perfection et enfin, lutter contre le gaspillage. Pour cela, la méthode s’inspire de la fameuse règle des “5 S”, à savoir cinq mots japonais qui, comme son nom l’indique, commencent par la lettre “s” et signifient : trier (Seiri) ; ranger (Seiton) ; nettoyer (Seiso) ; standardiser (Seiketsu) et respecter (Shitsuke). Revenons-en à nos gaspillages. À l’heure actuelle, on en liste sept parmi lesquels on retrouve notamment la production excessive, les temps d’attente, les stocks, les mouvements et transports inutiles ou encore les corrections apportées à l’objet.
Un planning collaboratif qui fait l’unanimité
Mais alors, comment le “lean management” peut-il s’adapter à la construction ? Peut-il améliorer les conditions de travail au sein des entreprises faisant partie de ce secteur ? Ces questions, l’Organisme professionnel de prévention du bâtiment et des travaux publics (OPBTP) se les est posées, dans un rapport dédié paru en avril 2021. Ce document se base sur des résultats obtenus lors de chantiers expérimentaux afin de proposer des pistes d’amélioration, et vient compléter une autre étude, intitulée “Lean construction – démarche d’optimisation de la production et de réduction des gaspillages sur chantier”, qui avait été menée en 2018 par la Fédération française du bâtiment Nouvelle-Aquitaine et l’OPPBTP.
Mais rien ne vaut quelques exemples d’application concrets : celui de la planification collaborative, baptisé dans le jargon “last planner system”, consiste à établir chaque semaine avec toutes les équipes un planning. Ce dernier réunit toutes les missions à exécuter, affichées à l’aide de post-it de couleur, positionnés ou retirés selon l’avancement du chantier. Autre exemple : les indicateurs de suivi. Ils se présentent en une liste d’objectifs à atteindre présentée de manière simple et visuelle. Chaque activité importante est liée à un indicateur dans le but de vérifier son avancement. Et puisqu’il n’y a jamais trop de bonnes nouvelles, les études menées sur les chantiers montrent également qu’une bonne gestion des flux a une incidence très forte sur les accidents tels que chute de hauteur et de plain-pied.
« Sécuriser ces flux en prenant en compte les déplacements des hommes, des matériels et des matériaux concourt considérablement à la diminution de l’accidentologie du BTP, indique Yves Chassagne, ingénieur prévention de l’OPPBTP, dans un communiqué. Et c’est notamment cela que permet le Lean Construction. Avec ces cas concrets, nous avons pu mettre en évidence les répercussions positives du Lean Construction si les déterminants sont bien respectés. »
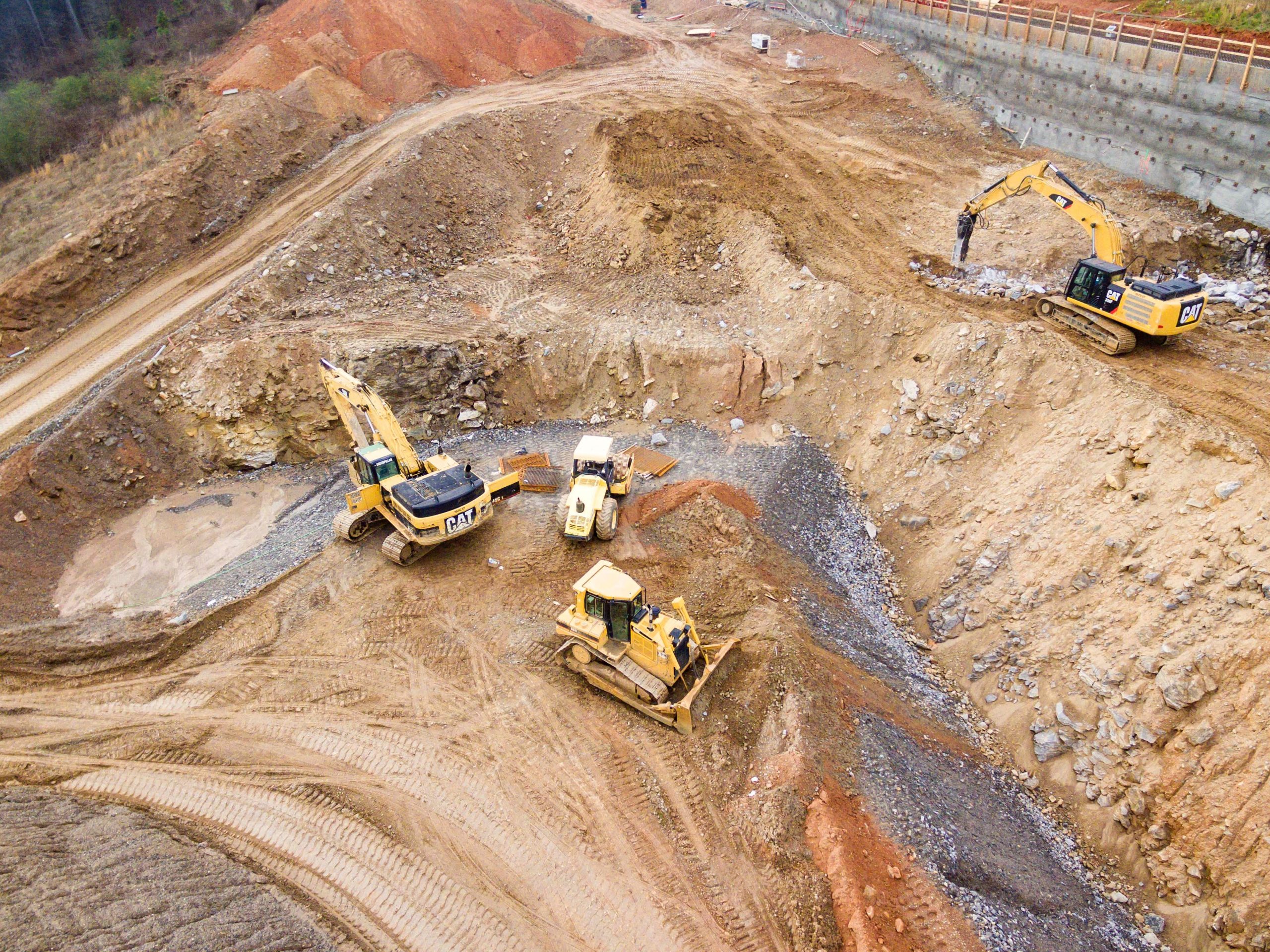
© Shane McLendon
À chaque problème, une opportunité
Qu’en est-il des petites entreprises et artisans ? Même traitement. Le “lean construction” n’est en aucun cas réservé aux plus grands. Si certains artisans ou TPE observent des dysfonctionnements, susceptibles d’être transformés en leviers d’amélioration, il serait bien dommage de ne pas utiliser ce système dont la devise pourrait être “tout problème devient opportunité”. C’est d’ailleurs pour cette raison qu’un nombre croissant d’entrepreneurs cherchent à s’initier auprès de consultants proposant des formations courtes. Les écoles et universités elles-mêmes reconnaissent les avantages de la pensée “lean” et l’intègrent dans différents cursus. Peut-être voient-elles en ce système un retour au bon sens ? Car vouloir prendre de la hauteur, perfectionner ses ressources humaines, financières ou matérielles afin d’obtenir le meilleur résultat et la performance la plus élevée… N’est-ce pas là le fondement d’une activité économique durable ? Auquel cas, la force du “lean construction” serait avant tout de se (re)poser les questions les plus rudimentaires.
Texte : Ana Boyrie
Visuel à la une : © Chris Mok
— retrouvez l’article sur le lean construction das Archistorm 117 daté novembre – décembre 2022